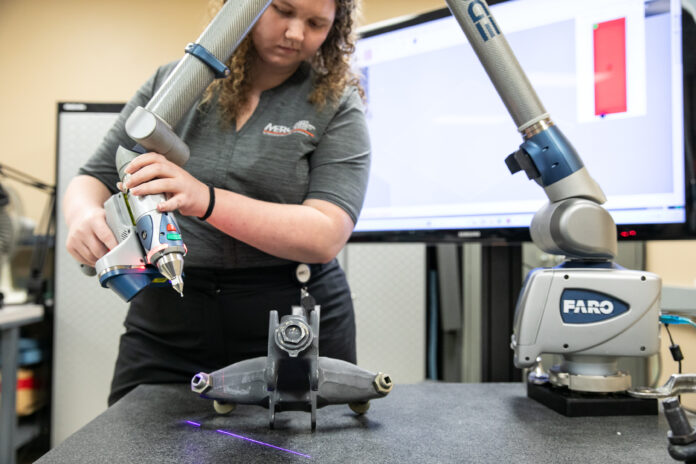
When the Air Force was looking to improve the safety and reliability of a rack that carries and releases bombs from aircraft, it turned to the Mercer Engineering Research Center for help.
Together, a small team of Air Force and MERC engineers redesigned critical components of the bomb rack on the B-2 stealth bomber to prevent unintended bomb release and mitigate damage to the bomb rack during training.
“What’s so rewarding about working for MERC is supporting the warfighter — the men and women who are out there every day protecting us,” said Andi Mitchell, executive director of MERC, a nonprofit operating unit of Mercer University.
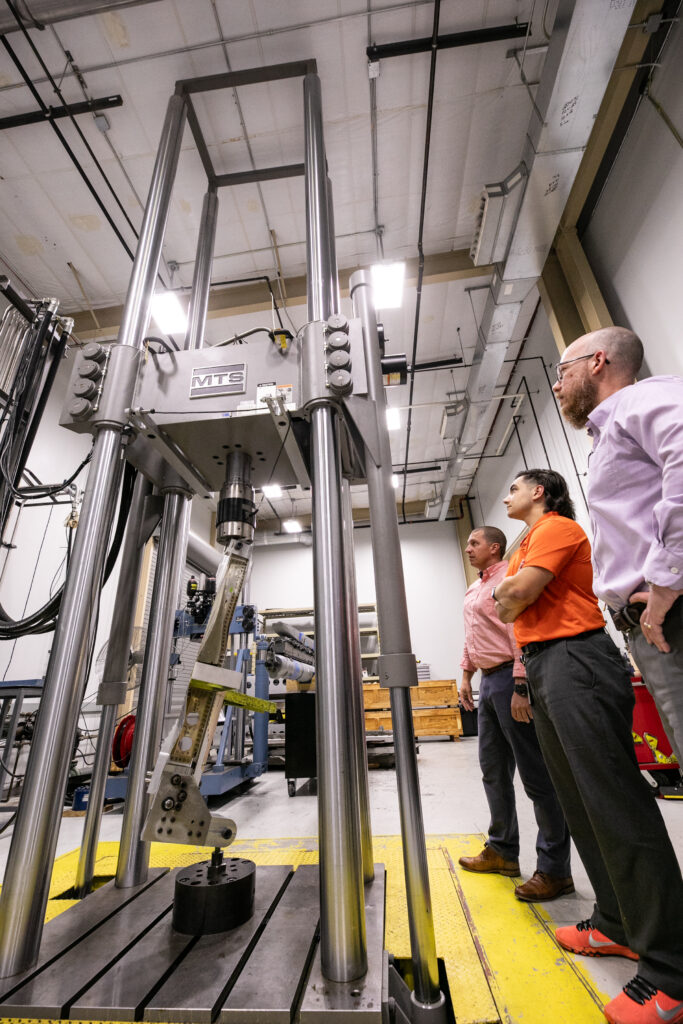
For 36 years, MERC has been providing real-world solutions to clients that include the Department of Defense; federal, state and local government agencies; major defense contractors; and commercial entities. Its 113,000-square-foot facility is located in Warner Robins, 5.5 miles from Robins Air Force Base, which is MERC’s primary customer.
In the early 1980s, Maj. Gen. Cornelius Nugteren, the two-star commander at Robins, approached Mercer with concerns about a shortage of engineers and asked the University if it could establish an engineering program. Mercer founded the School of Engineering in 1985, and MERC opened two years later with three employees and an $8,400 contract.
MERC’s core capabilities include aerospace, electrical, mechanical, software/cyber, and industrial engineering; electronic warfare; artificial intelligence/machine learning; reverse engineering and prototyping; and modeling simulation and optimization.
Many of MERC’s projects involve improving the life-expectancy and safety of aircraft; developing new and innovative repairs; designing new parts, devices, systems and software; and examining and recommending maintenance procedures, said Jim Hundley, senior director for engineering and programs at MERC.
The goal is to save clients time and resources while ensuring safety, Hundley said.
For example, MERC worked alongside the Air Force to examine the effects of gunfire blast on the AC-130W gunship during operation of the aircraft’s weapon. As a result, Air Force engineers have a better understanding of the impact the weapons system has on the plane’s structural life.
“Through advanced structural analyses and testing of these systems, MERC and the Air Force have established a trusted methodology for evaluating and maintaining these complex systems that have helped pave the way for the next generation of gunships,” Hundley said.
MERC is also a nationally recognized center of excellence in finite element analysis of military aircraft such as high-performance fighter jets, military cargo aircraft and helicopters.
MERC’s relationship with Mercer is mutually beneficial, Mitchell said. MERC employees may serve as adjunct faculty at Mercer, and MERC provides internships for University students. Also, several Mercer faculty members work on projects with MERC.
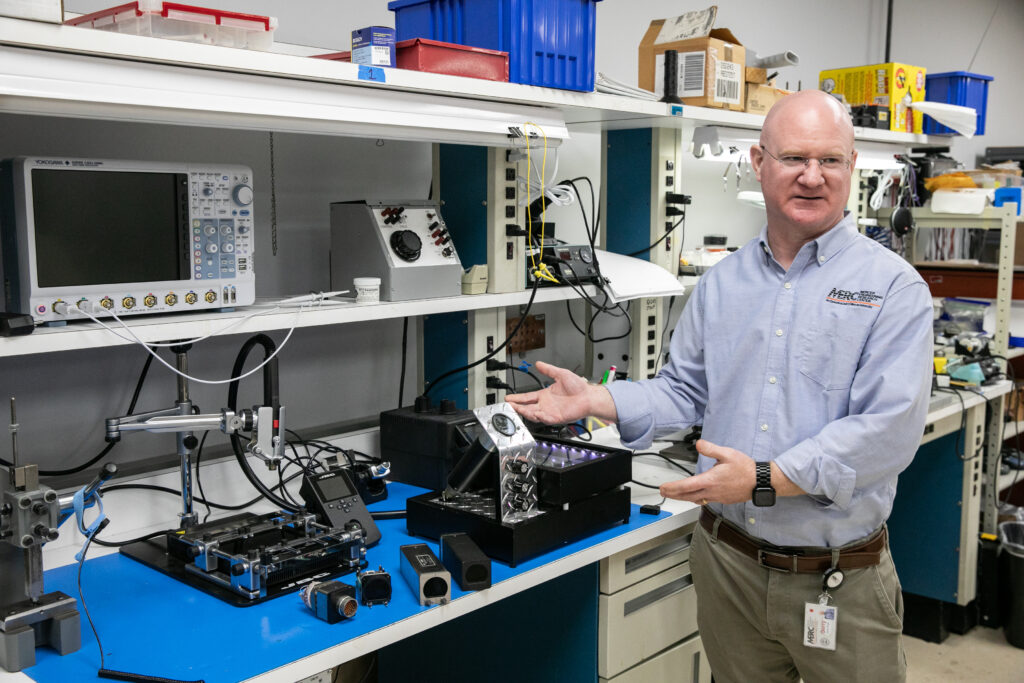
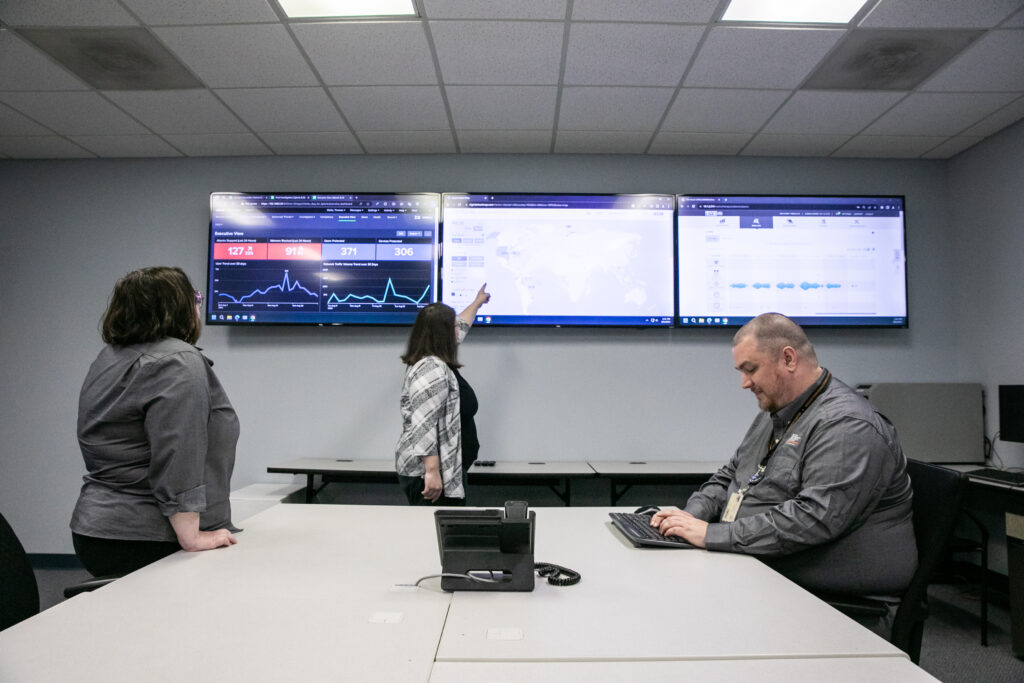
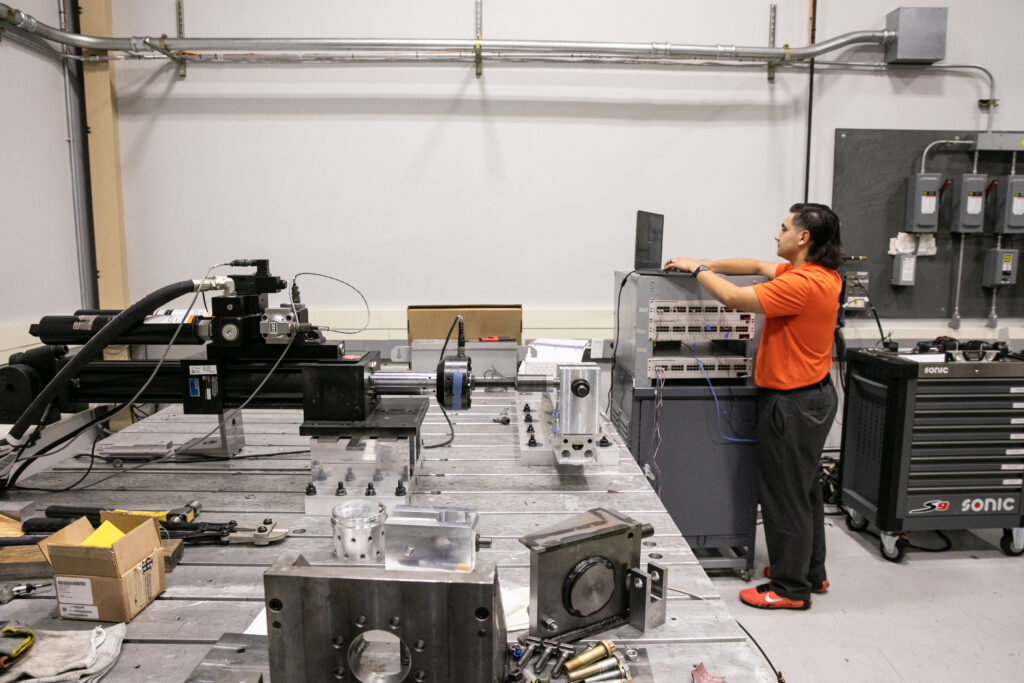
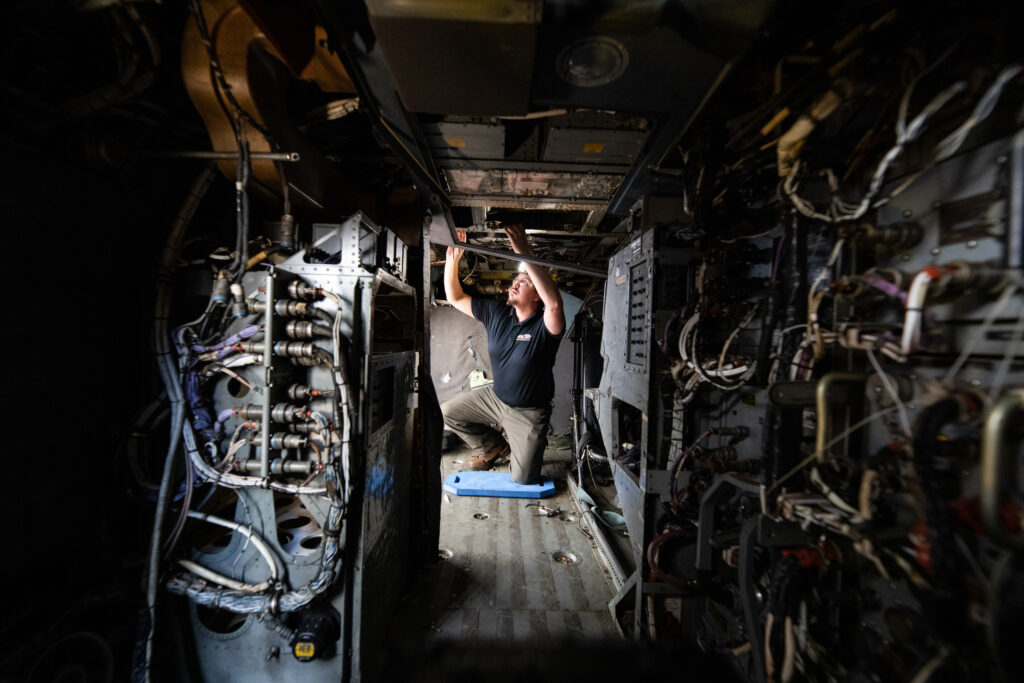
Chemists study impact of corrosion
Dr. Kevin Bucholtz, professor of chemistry, and Dr. Joseph Keene, associate professor of chemistry, have worked with MERC since 2018 on projects related to corrosion and how it affects the life and maintenance of ground support equipment in the Air Force.
Their research resulted in recommendations to use new materials or different applications of existing materials that would extend the equipment’s life, minimize downtime and increase war readiness, Dr. Keene said.
Corrosion costs the Department of Defense $20 billion annually, he said. But in addition to dollars, corrosion also costs time.
“The commanders want everything to be ready to go at the drop of a dime,” he said. “And if something is pulled off to the shop and it’s pulled apart because it’s being refurbished — sandblasted and repainted and reassembled — it’s not ready to go. … It’s also a war readiness issue.”
Dr. Keene and Dr. Bucholtz, who are housed in the College of Liberal Arts and Sciences, have since received a grant that enables them to continue their work outside the confines of a laboratory.
“This allows us to address one of the big disconnects that we observed between the laboratory or the simulated environment versus what’s actually happening in the real world,” Dr. Keene said. “We were able to acquire eight pieces of portable, hand-held instrumentation and laboratory equipment to basically take the research lab out into the field so that we can collect data and analyze the actual pieces of equipment in the environment where they’re actually corroding.”
They’re also working on another project with MERC that examines the decontamination procedures for the C-130 after exposure to chemical, biological, radiological or nuclear warfare.
“It’s been nice to have this real-world application for what we’ve been working on and allowing my students to get that experience — not just gaining the research experience but able to do it with a direct, real-world application,” Dr. Keene said.
Student participation has included visiting sites, analyzing data, writing reports and attending meetings to present findings, he said.
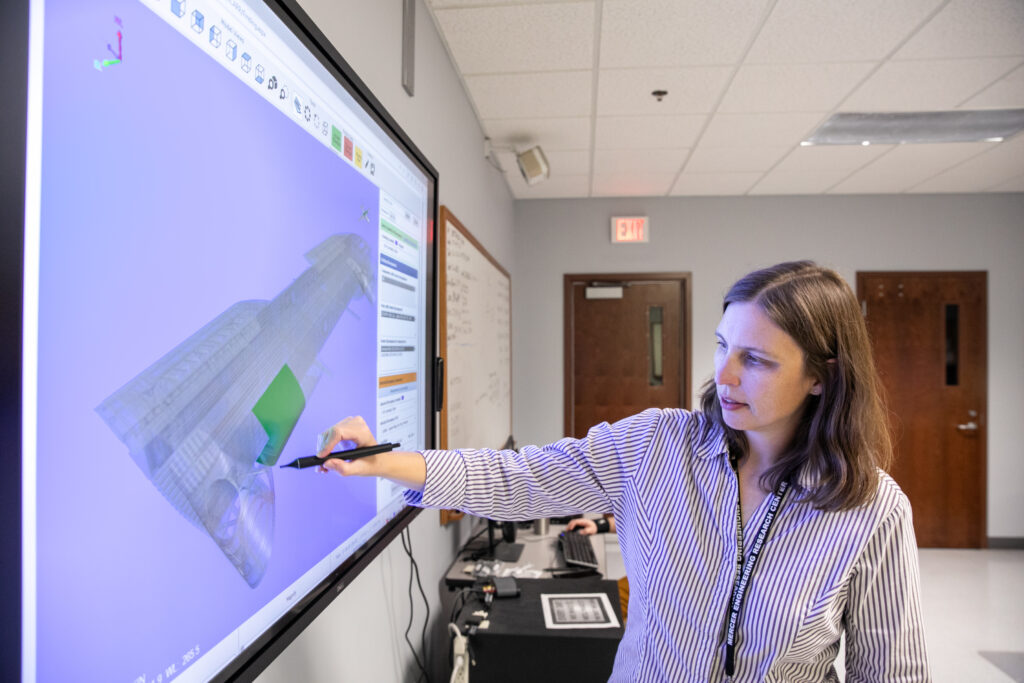
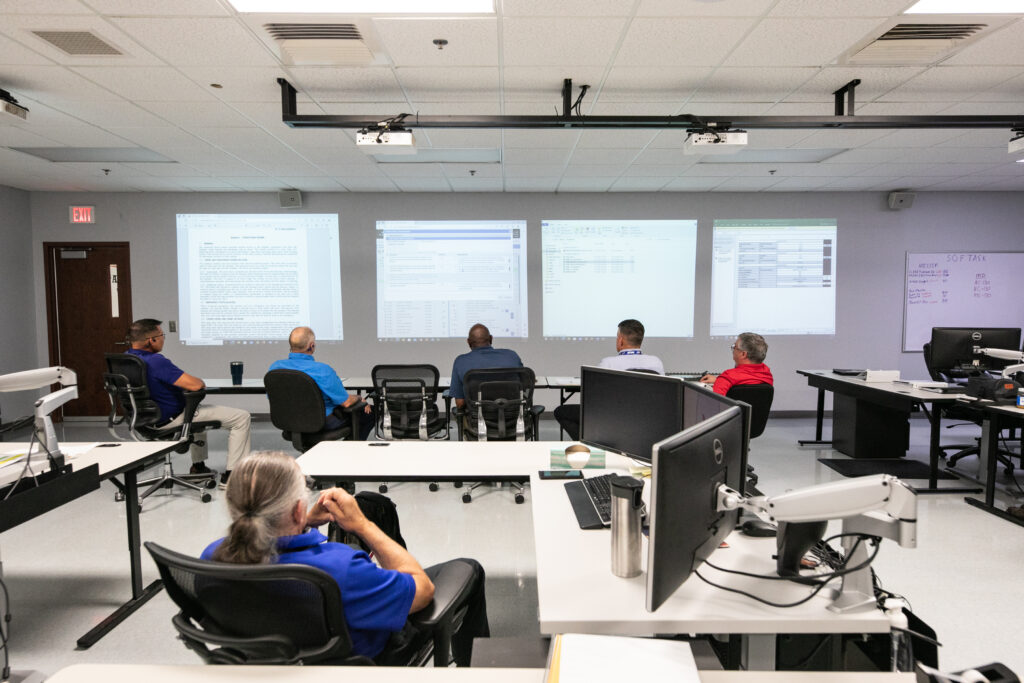

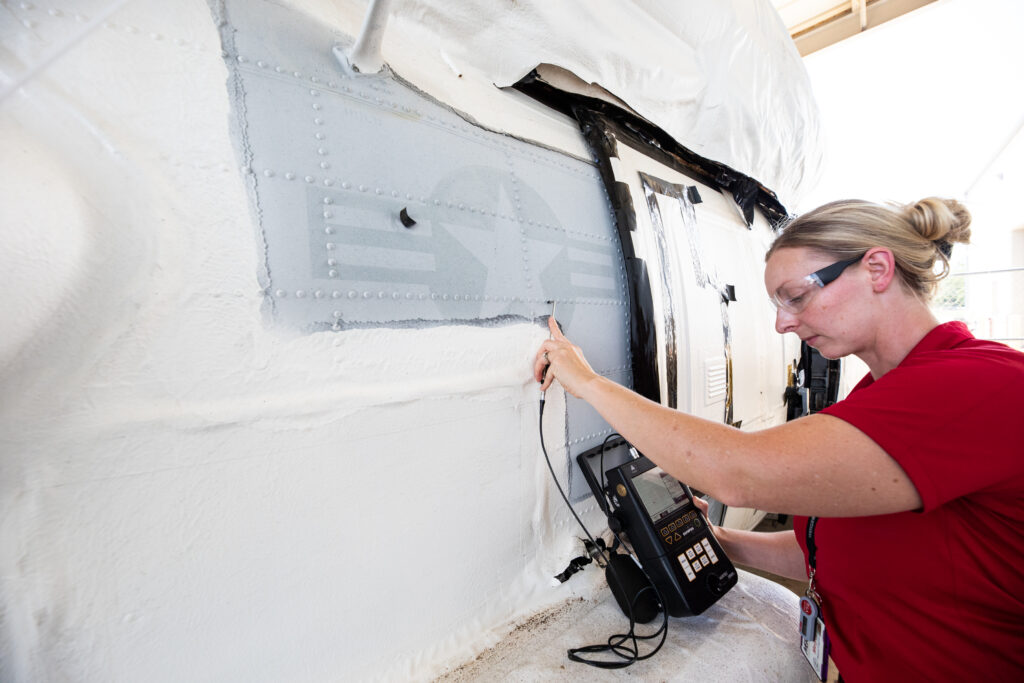
Engineer works on quadcopter, AI projects
Dr. Anthony Choi, professor of electrical and computer engineering, also has worked with MERC for several years.
One early project involved Mercer students designing and programming a prototype quadcopter drone, which is a drone with four propellers. Students from Middle Georgia State University built the platform and structure.
While this type of drone is now readily commercially available, that was not the case at the time, Dr. Choi said.
“The goal of this project was to build a quadcopter that had payload capabilities that were different from what was available,” he said. “It was also to prototype control systems, flight controllers and other programming to be able to build custom quadcopters. …
“This was a test platform to say that this type of quadcopter, this size and this weight, can be built and then tested for future missions. The application of the missions could have been surveillance, reconnaissance, search and rescue, or various other things.”
More recently, Dr. Choi has been involved in a project, Rosetta Stone, that allows different systems to communicate with one another. He was instrumental in developing a large language model, like those used in artificial intelligence, that was the basis for the project.
In the past, “it took humans to actually read through written text descriptions and other types of things, and it needed human experts who understood the system to be able to do all these mappings by hand,” said Dr. Choi, who is director of the Machine Intelligence and Robotics Laboratory at Mercer. “What we did was develop a computer system that would actually read the text and be able to map that automatically without needing a human expert.”
Dr. Choi said he has had many students help with MERC projects. One student became so vested in the Rosetta Stone project that he went on to work for MERC after graduation.
“To get that type of experience is very exciting for the students,” Dr. Choi said. “It’s not just theoretical work. It’s not just a project. This is a working system that the Air Force currently needs, and it’s actually going to make a difference.”
The Rosetta Stone project was funded by the Defense Advanced Research Project Agency, or DARPA, a research and development agency of the Department of Defense.
“Rosetta Stone enabled Air Force personnel to identify replacement parts for the C-130 within minutes, rather than hours or days, which reduced maintenance costs by hundreds of thousands of dollars,” said Steve Boswell, MERC’s technical lead for the project.
Today, MERC has over 200 employees and nearly $700 million in new contract awards to date, Mitchell said.
“We’re Mercer’s best kept secret,” she said. “We are proud to be a major contributor to the University’s research initiatives.”